This research focuses on the use of a new material : the cellular glass produced from 100% recycled glass by the German company Glapor. The objective is to diversify the application of Glapor products within construction details, moving beyond their mere function as insulation to also leverage their remarkable compressive strength. We thus present a non-exhaustive catalog of construction details where Glapor panels serve as load-bearing elements, contributing to the design of walls, floors, roofs, etc. This catalog provides an overview of the opportunities presented by this material while highlighting its inherent limitations and exploiting its qualities listed below.
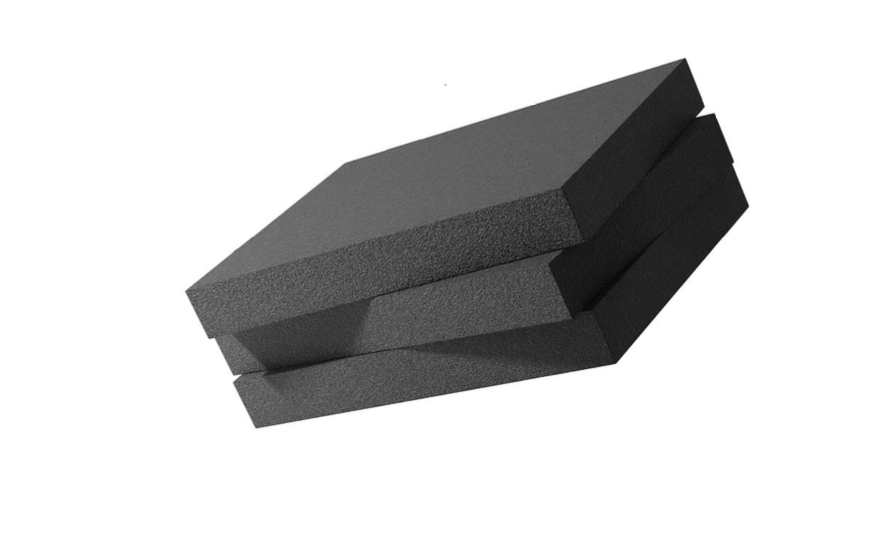
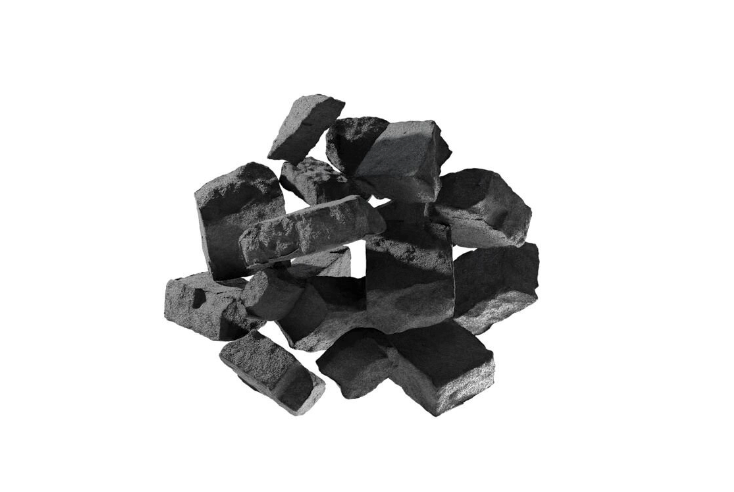
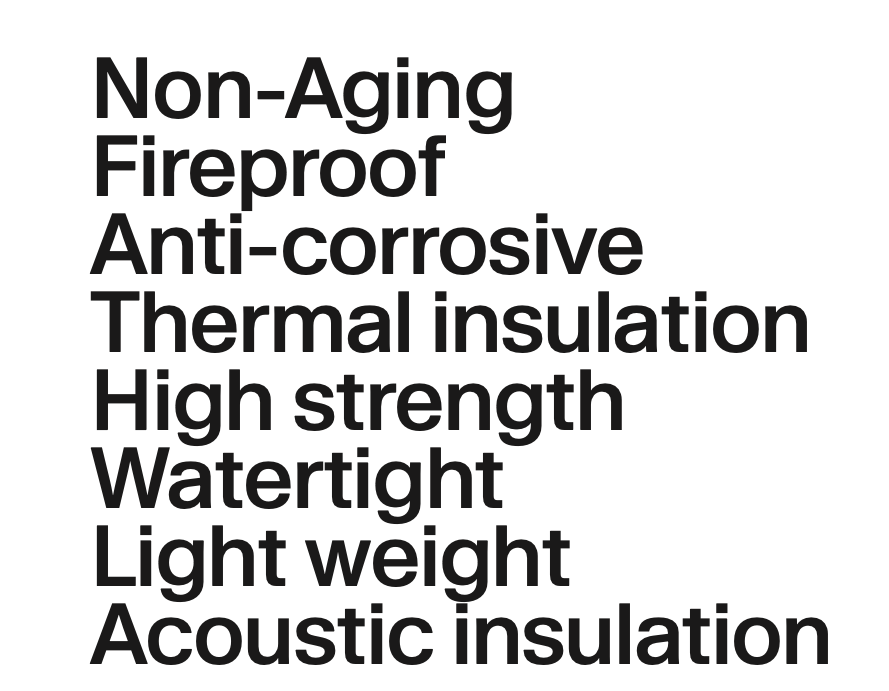
Our primary work has been to enable the use of GLAPOR panels as structural elements, either through simple layering and compressing or through a “brick-laying” technique. Additionally, this can be reinforced using bracing that can also serve as cladding.
Our goal was to develop details using dry assembly and that don’t perforate the GLAPOR boards, manily through clamping. For the wall and floor elements, aside from the recycled glass material, we limited ourselves to wooden frames and cork assembled with straps and screws. For the roof details, we add steel profiles, to resemble hollow-core slabs, when the potential forces acting on the structure become too substantial. Regarding the connections between walls, the concept is to protect the corner by offering various connector elements while facilitating the installation process.
(1) Walls
Our wall system is inspired by the technique used to build straw walls. Glapor panels are compressed between two wooden panels using a ratchet strap. Each panel is separat- ed by a textile element that allows them to adhere to each other.
The size of the panels is adaptable. Here, the dimensions al- ready marketed by Glapor are used. Although large panels are preferable for their practicality, care must still be taken to design a solid wall. So, as their height cannot be too great, the panels all have a size of 80 x 30 x 12cm.
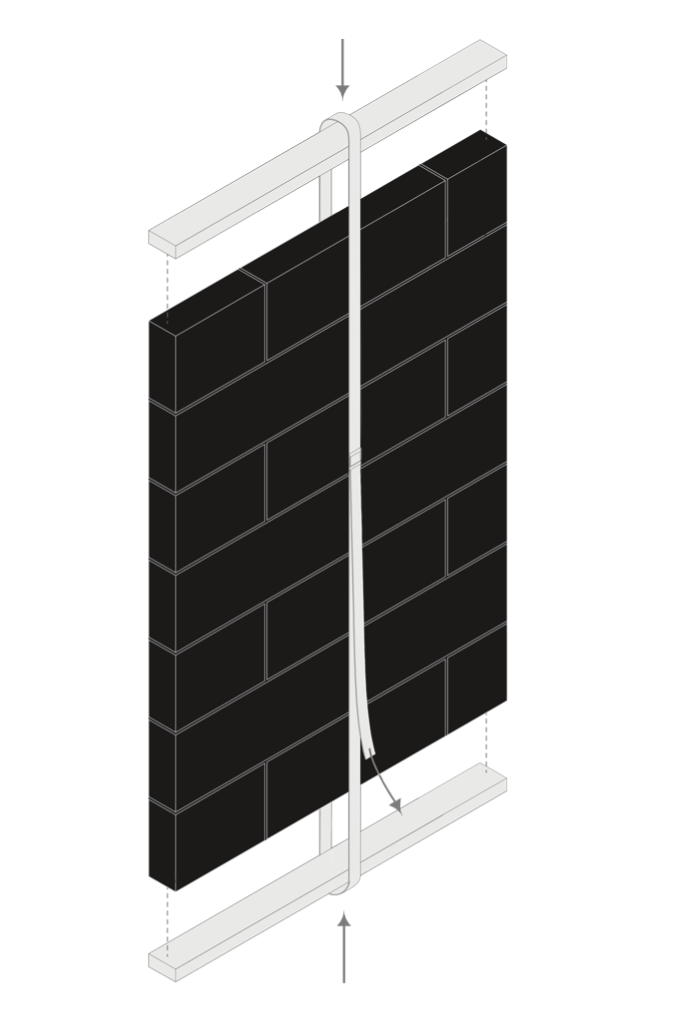
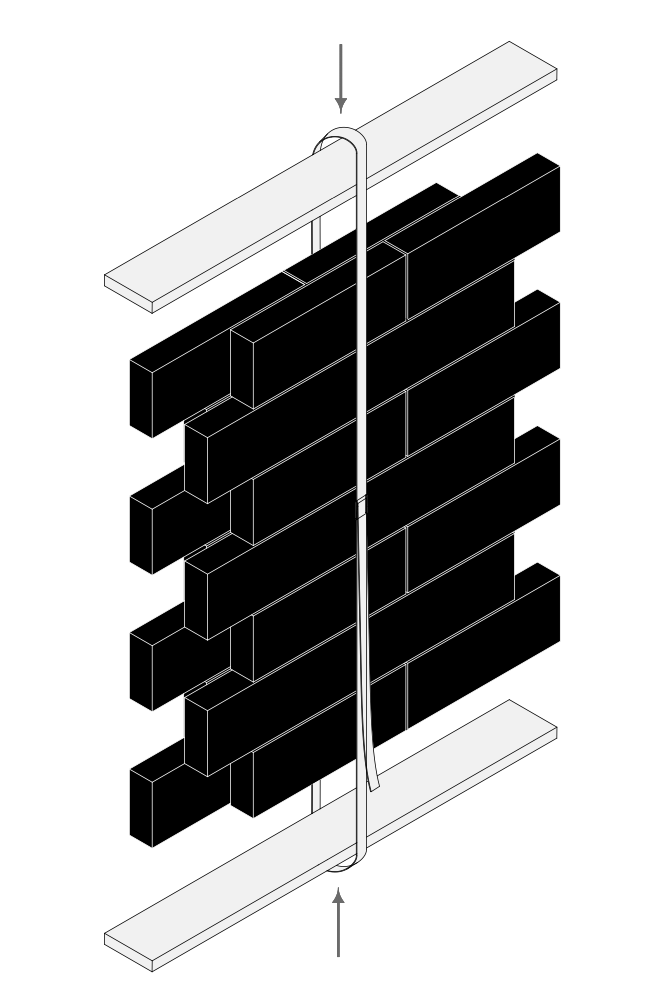
(2) Bracing and Cladding
This simple cable metal cladding enables an extra tension to fit the bricks together, as well as bracing against external forces. Screwed to wooden pan- els on the exterior, it leaves the GLAPOR material intact. This method, as well as the other cladding methods, can be addapted to the connections they are used in, adapting to the use and form the wall takes. It however has the disadvantage of not offering a a covering of any sorts, leaving the material open to impacts and damage. This can be reduced by adding a coating of GLAPOR-Waterglass mixture to the surface of the panels.
Vertical and horizontal beams present a traditional way of reinforcing the wall, and offer a ideal structure for wooden exterior cladding or ceramic fa- cade elements as seen here. Screwed together, these wooden elements easily attached to the top and bottom compression beams, as well as the vertical joints on the side.
In regards to the metal cladding, this wooden panel cladding offers a rein- forcement of the compressive forces on the GLAPOR, all while presenting an alternate surface that can be used for coating and finitons. When adding a distance between the panel and the compressed material, this solution per- mits a void that can be used for electicity or plumbing installations.
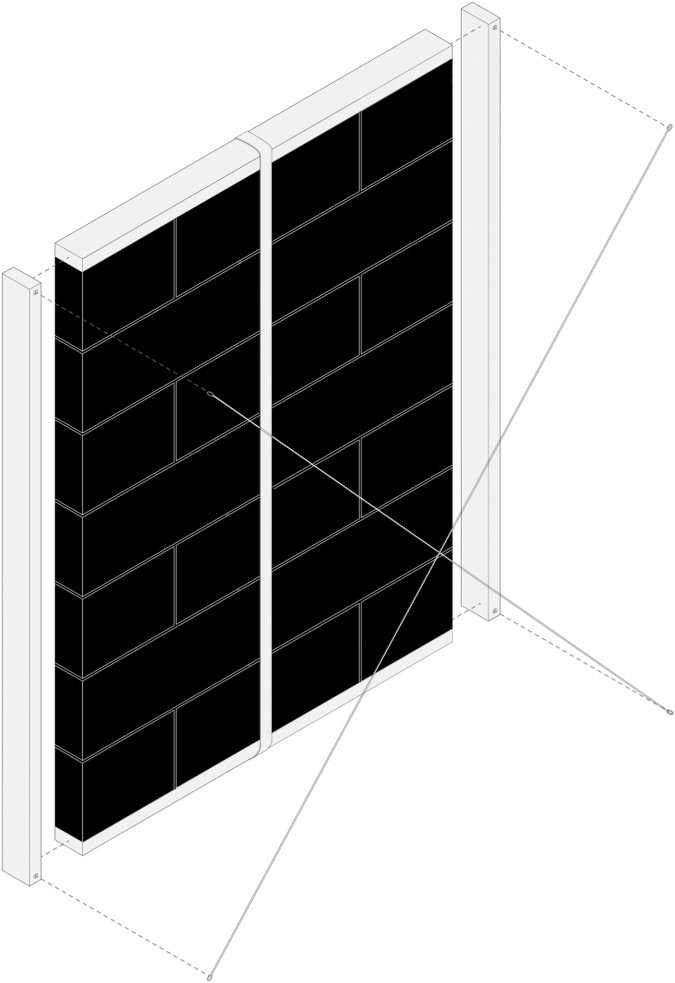
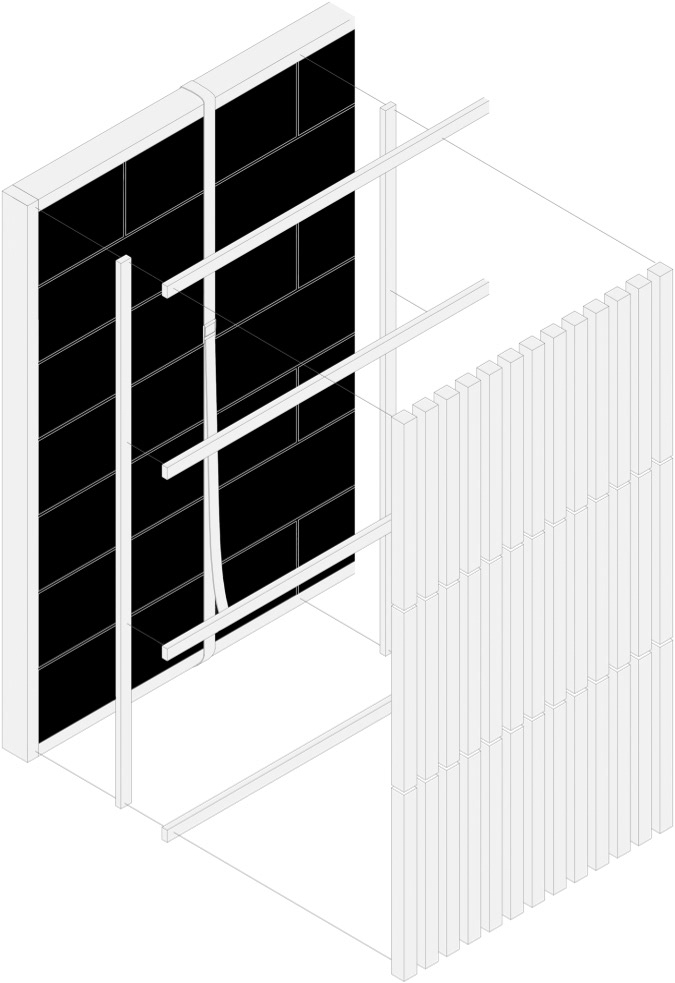
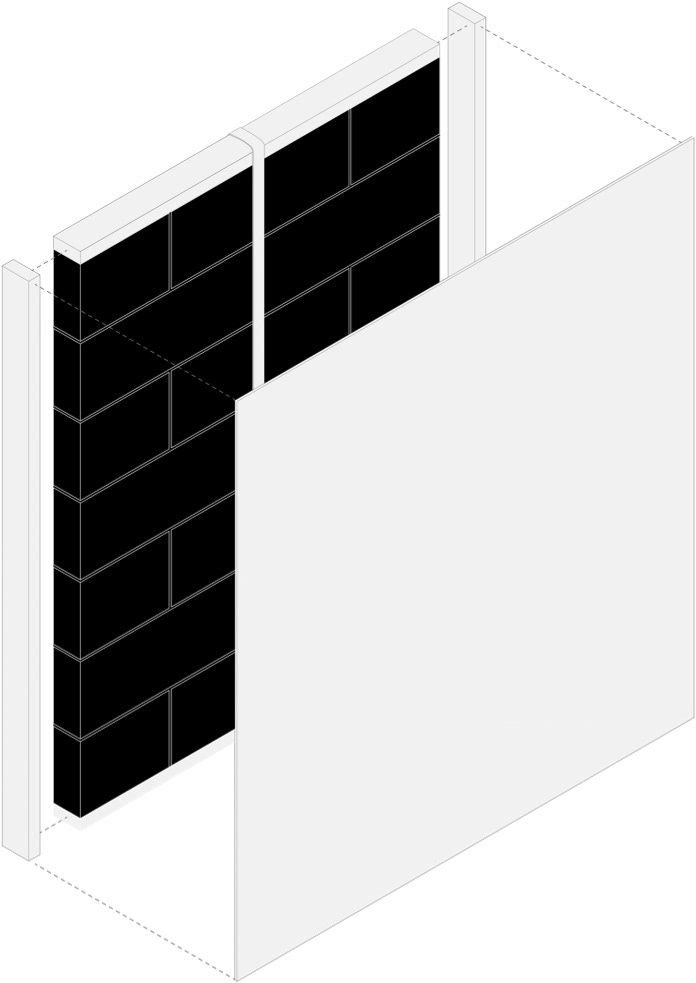
(3) Floor
The floor is made up of two layers of Glapor panels, oriented perpendicular to each other and wedged between wood- en beams. As it is not subject to horizontal forces, panels of maximum dimensions can be used without risk.
However, the surface of the Glapor panels remains fragile, making it preferable to cover them with parquet, which is fixed to the wooden beams.
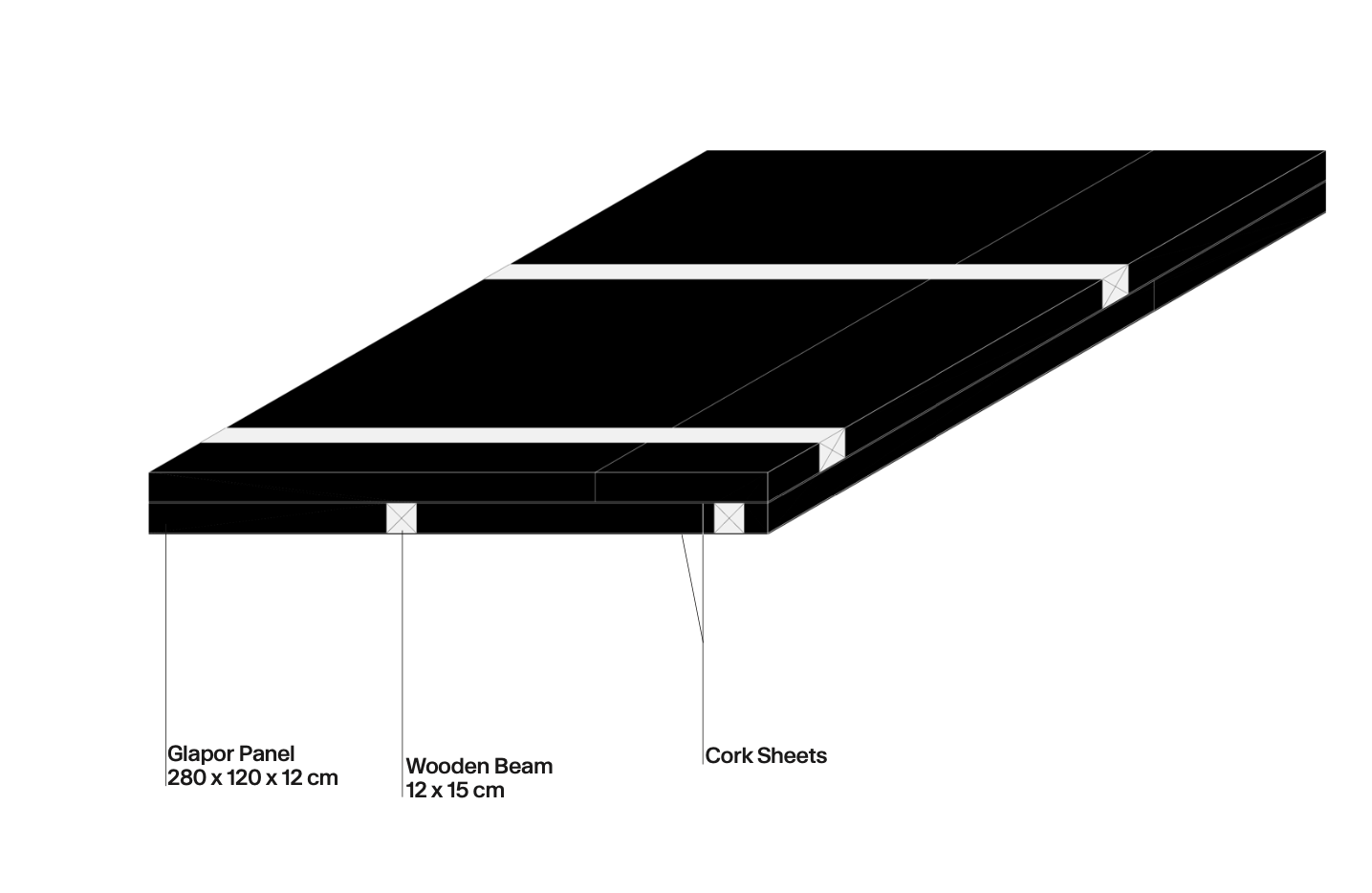
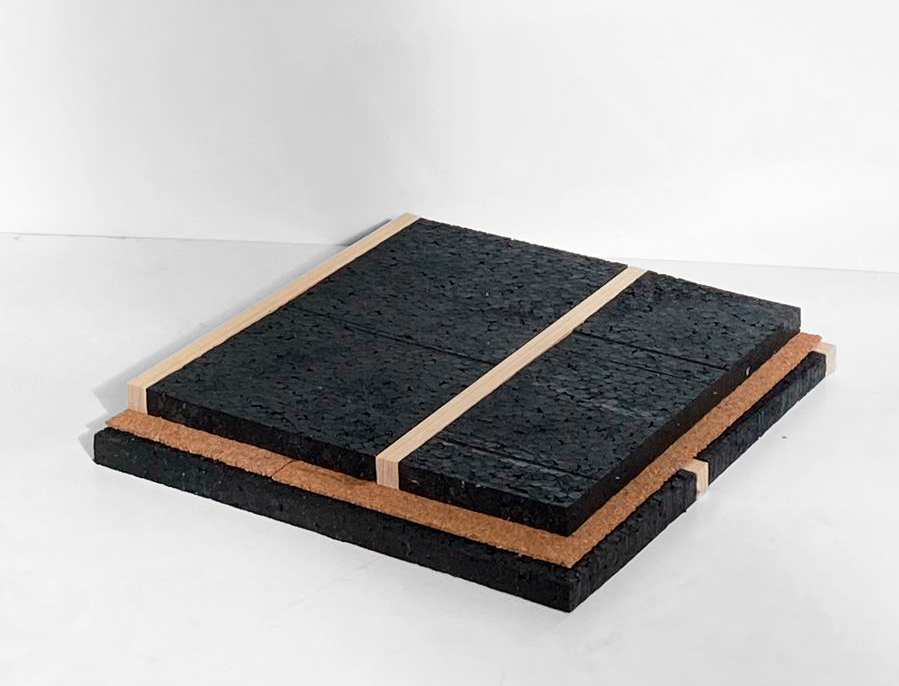
Floor made out of 2 layers of Glapor panel fastened between wooden beams and protected from water by two layers of cork. Serving as support and potential covering with parquet.
(4) Roofs
The roof construction details are inspired by the hourdis system. It can be used for both flat and pitched roofs. For small spans, it is also possible to use a compression system if the roof is not load bearing.
The roof elements are fixed to the wall on the wooden beams that enable the compression.
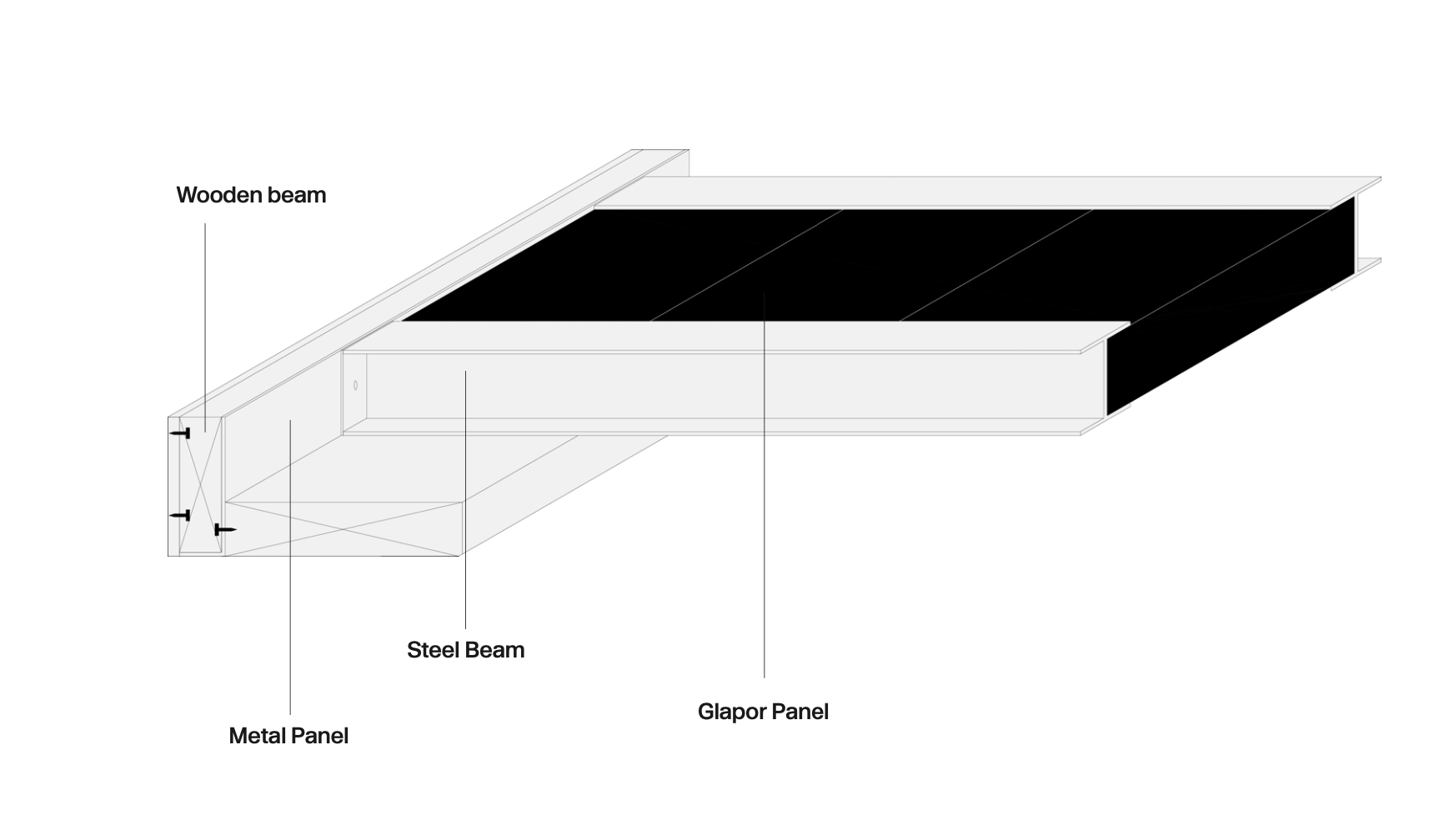
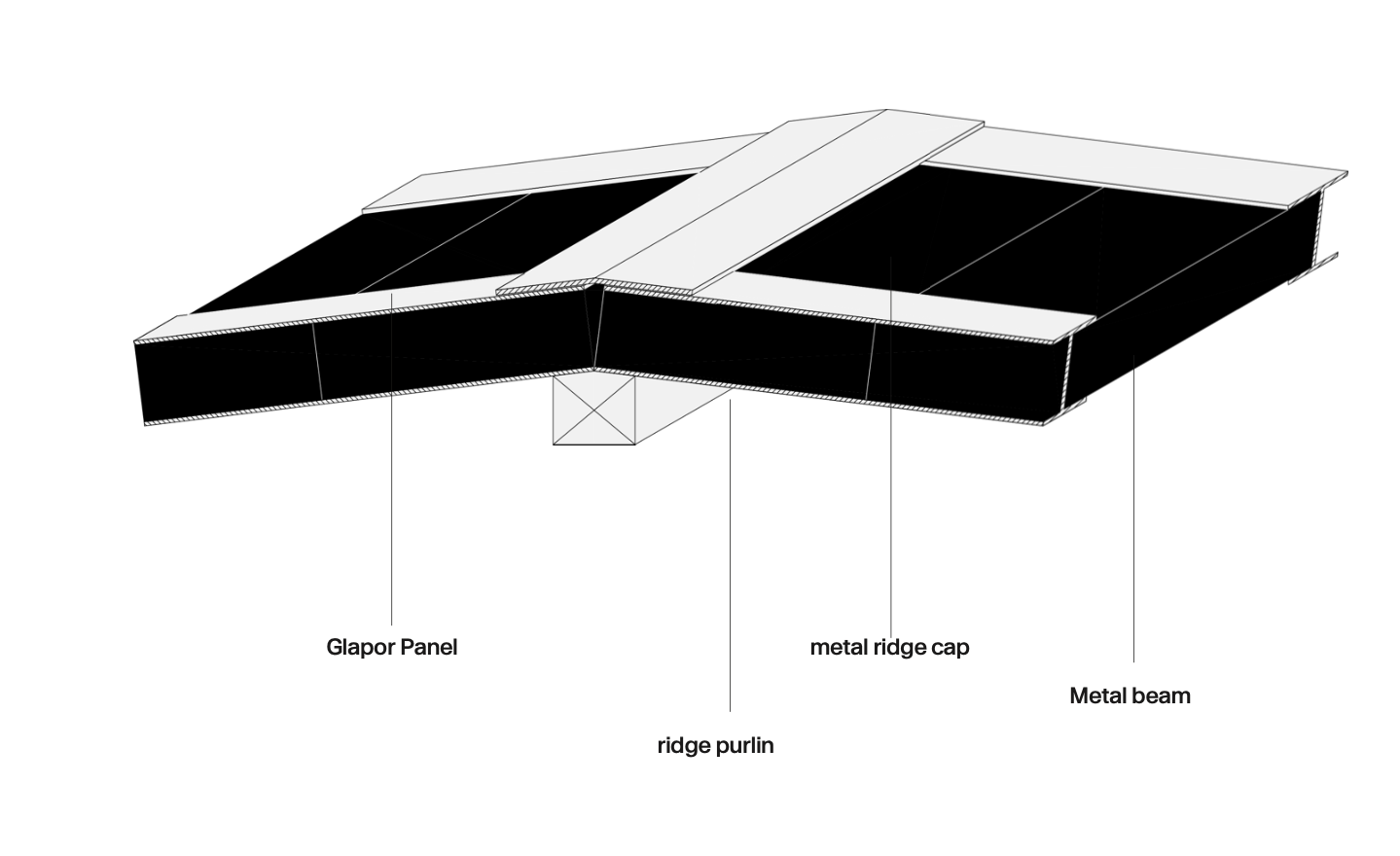
(5) Connections
The joint details below are made up of two layers of Glapor panels, held in compression either uncoupled or grouped together. In this way, the first detail has the advantage of being easy to install, while the second, although less practical, is stronger and more compact.
The second detail is also protected at the corner. The junction of the two walls is achieved thanks to the recess offered by the qincunx arrangement of the panels.
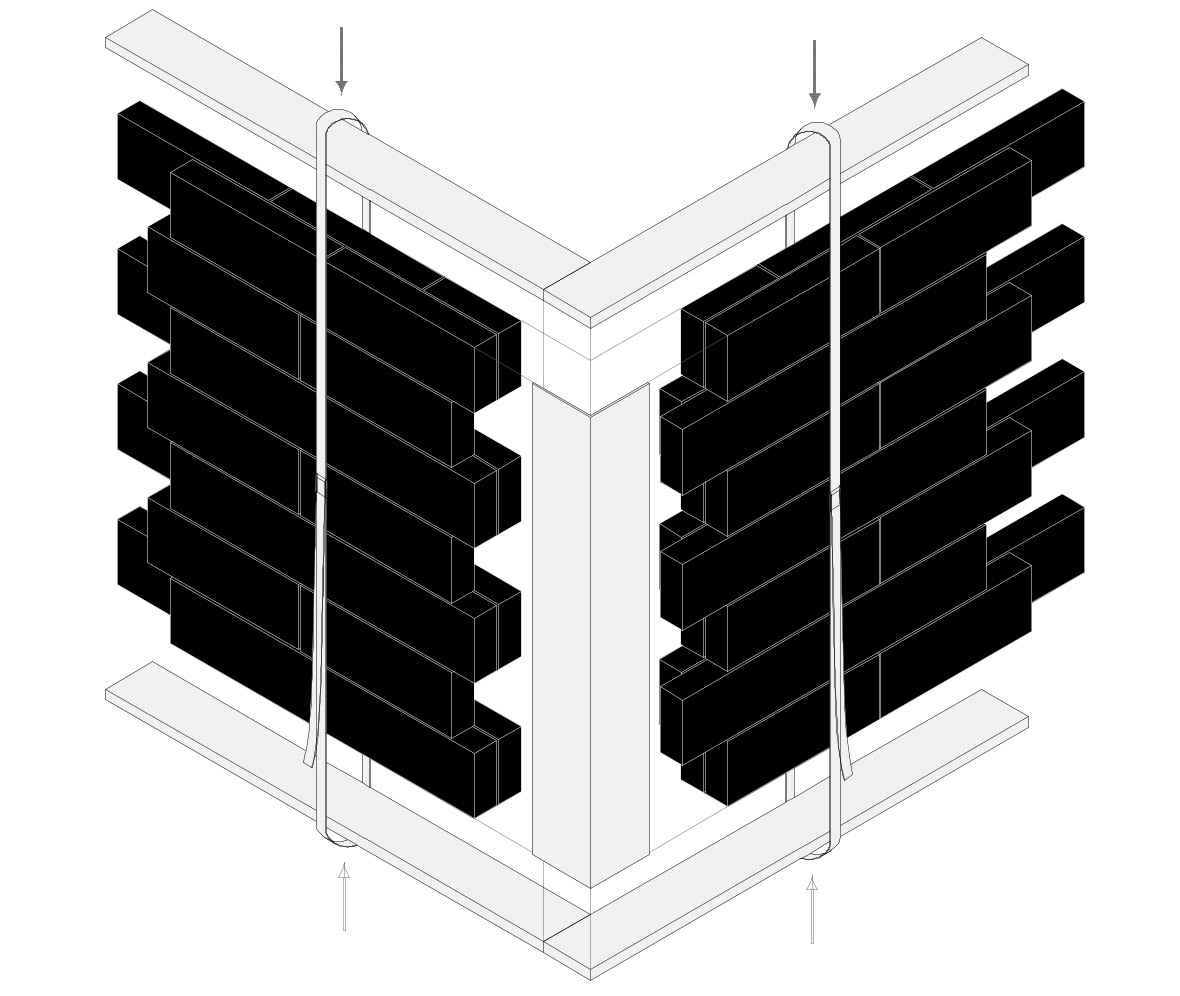
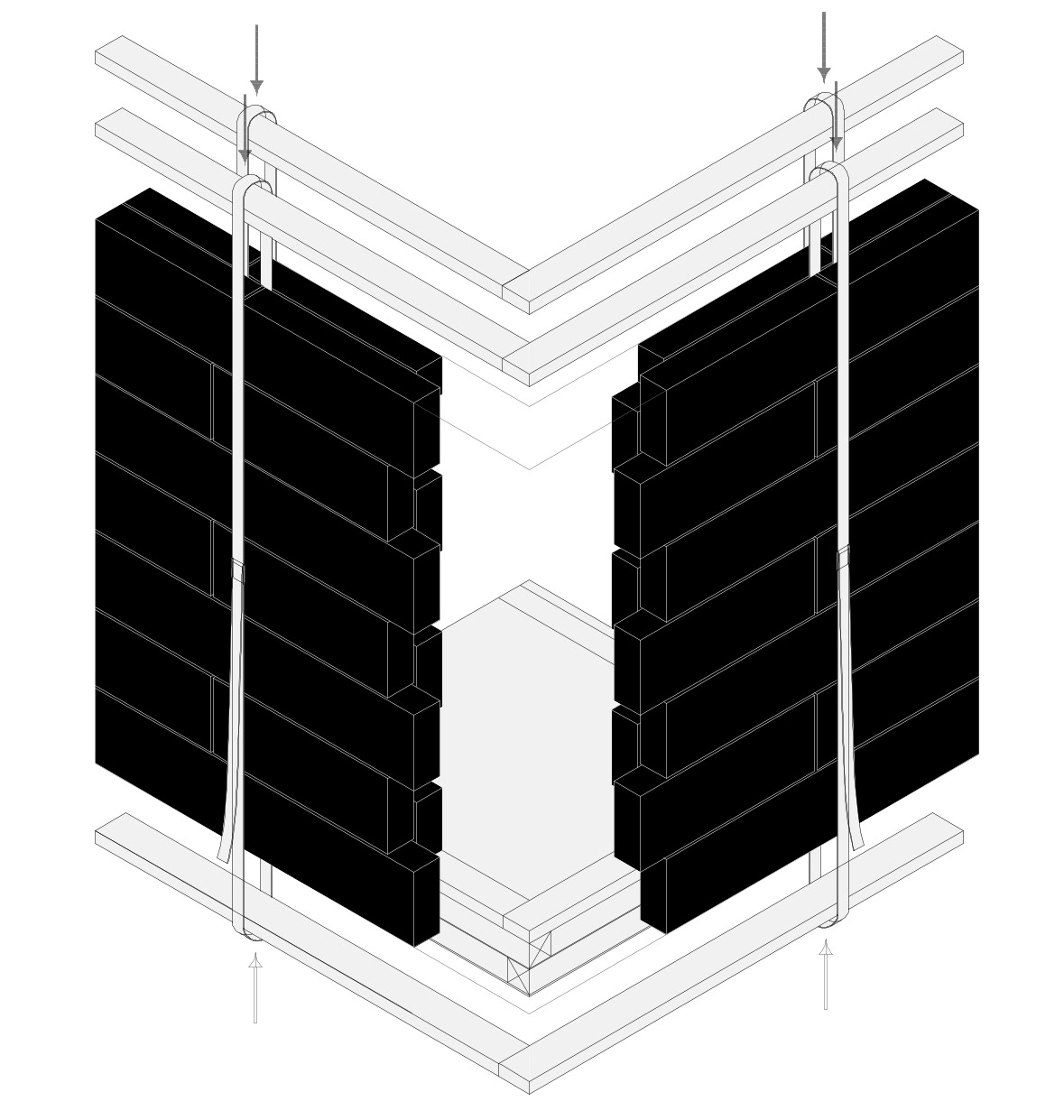
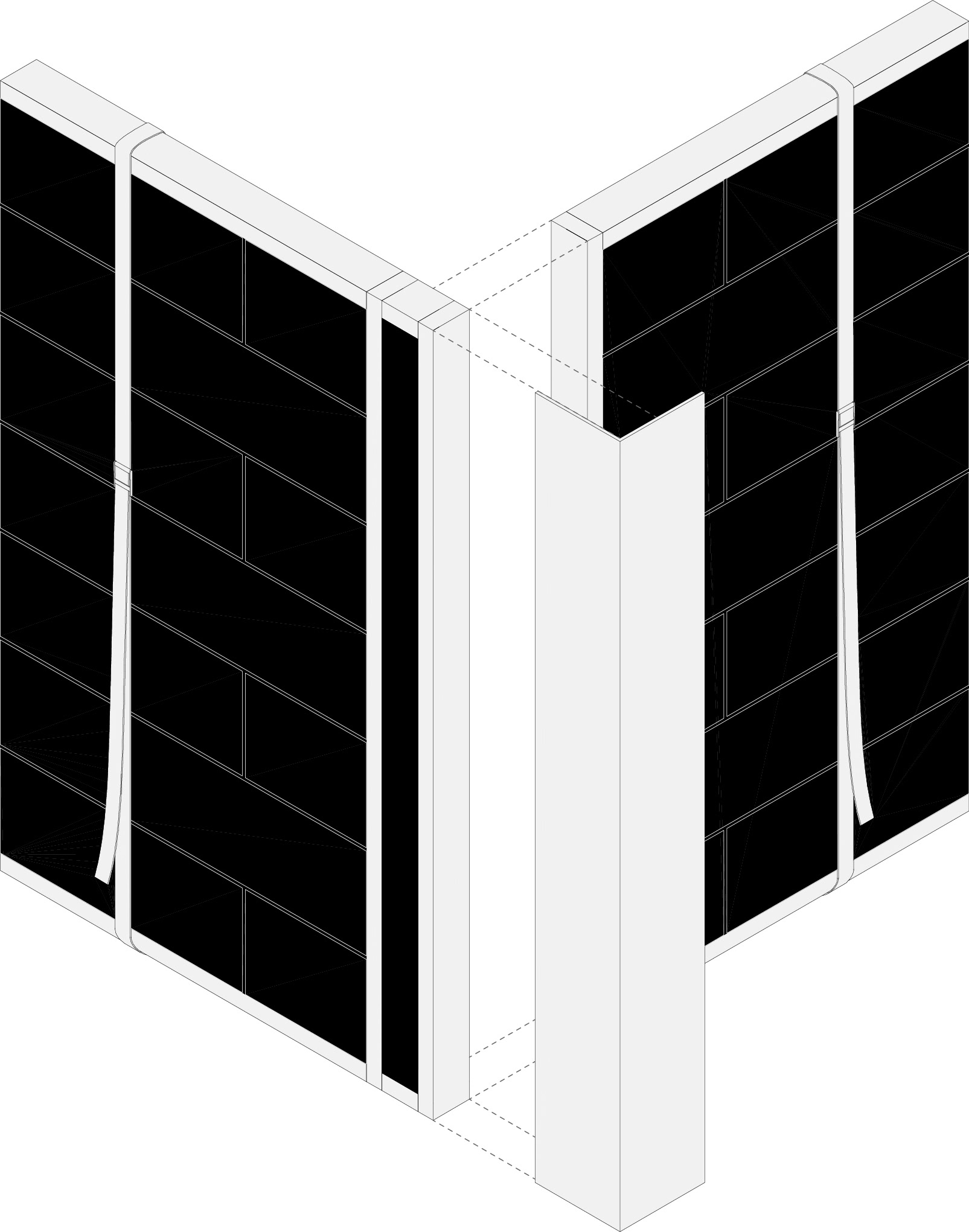
The junction is inspired by the angles used in timber-framed wall con- struction. A wooden profile is added to protect the joint properly.
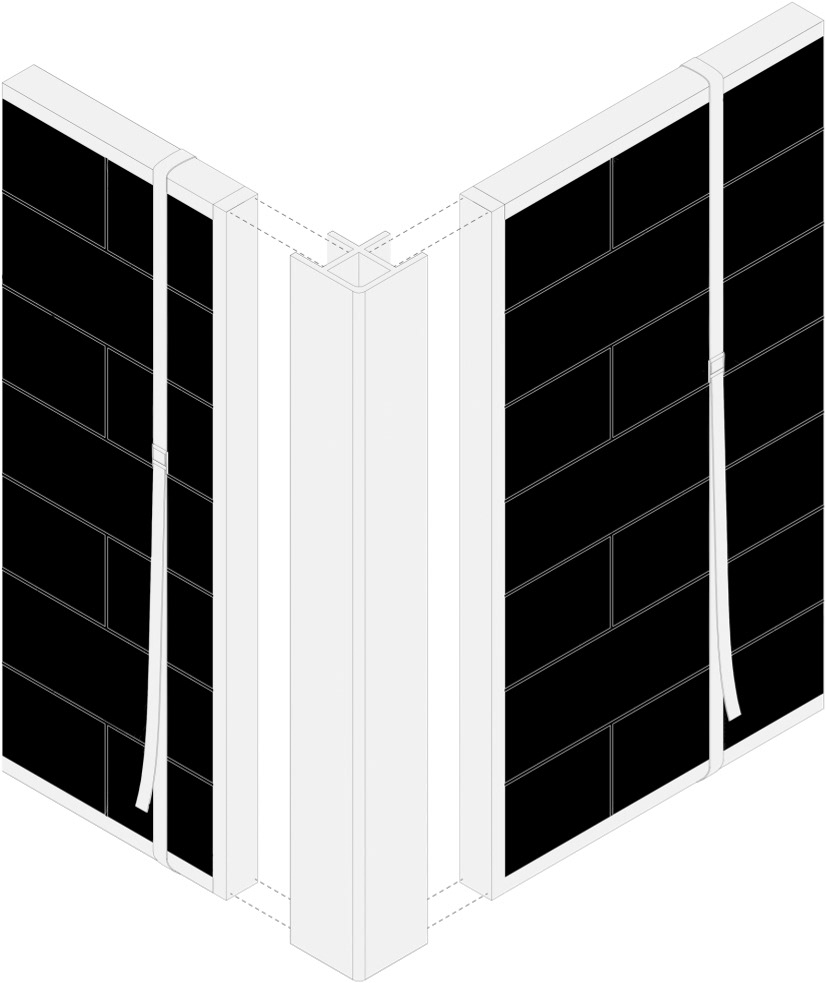
One piece wall to wall connection out of metal, fastened to the wooden frame of the wall.
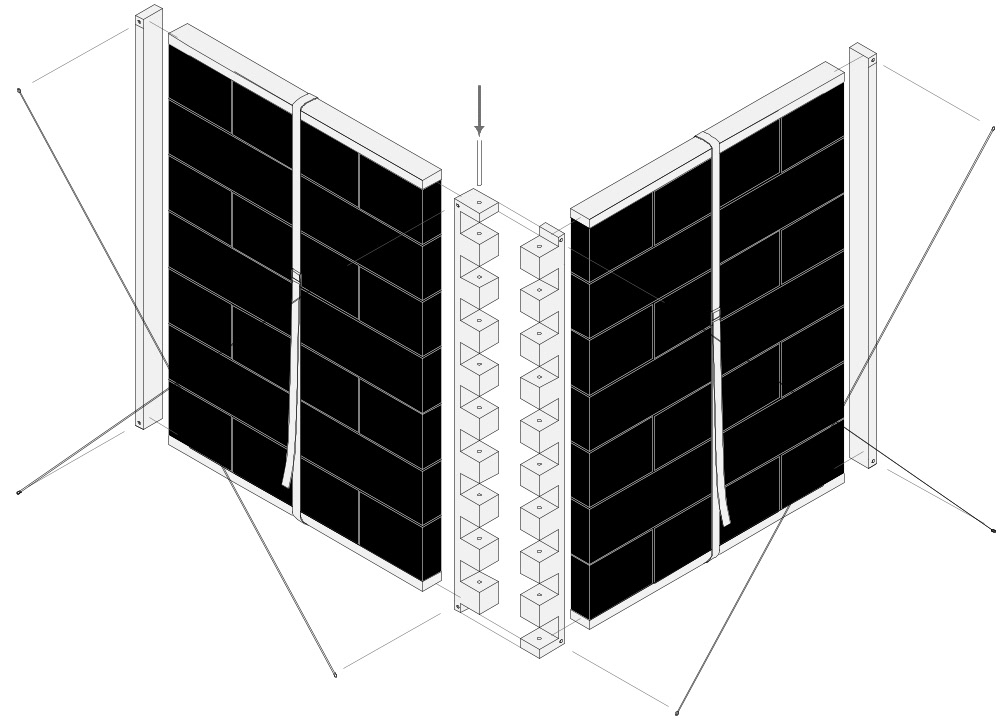
Single wall wooden joint connection, attached to each wall seperately and locked in place with each metal rod
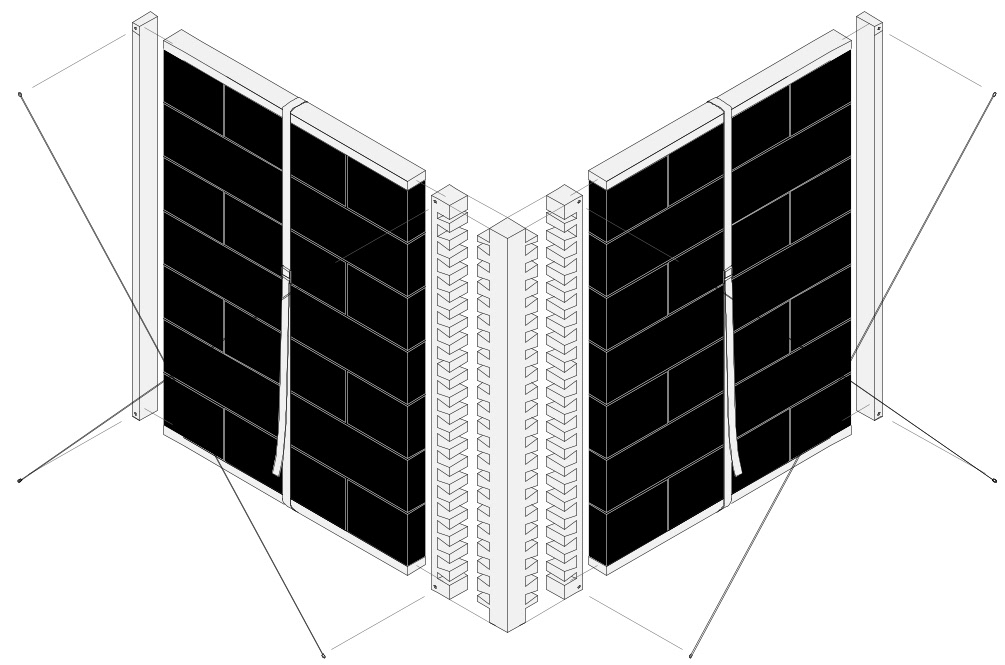
Single wall wooden joint connexion, attached to each wall seperately and fastened with a sliding wooden piece.
(6) Assessment
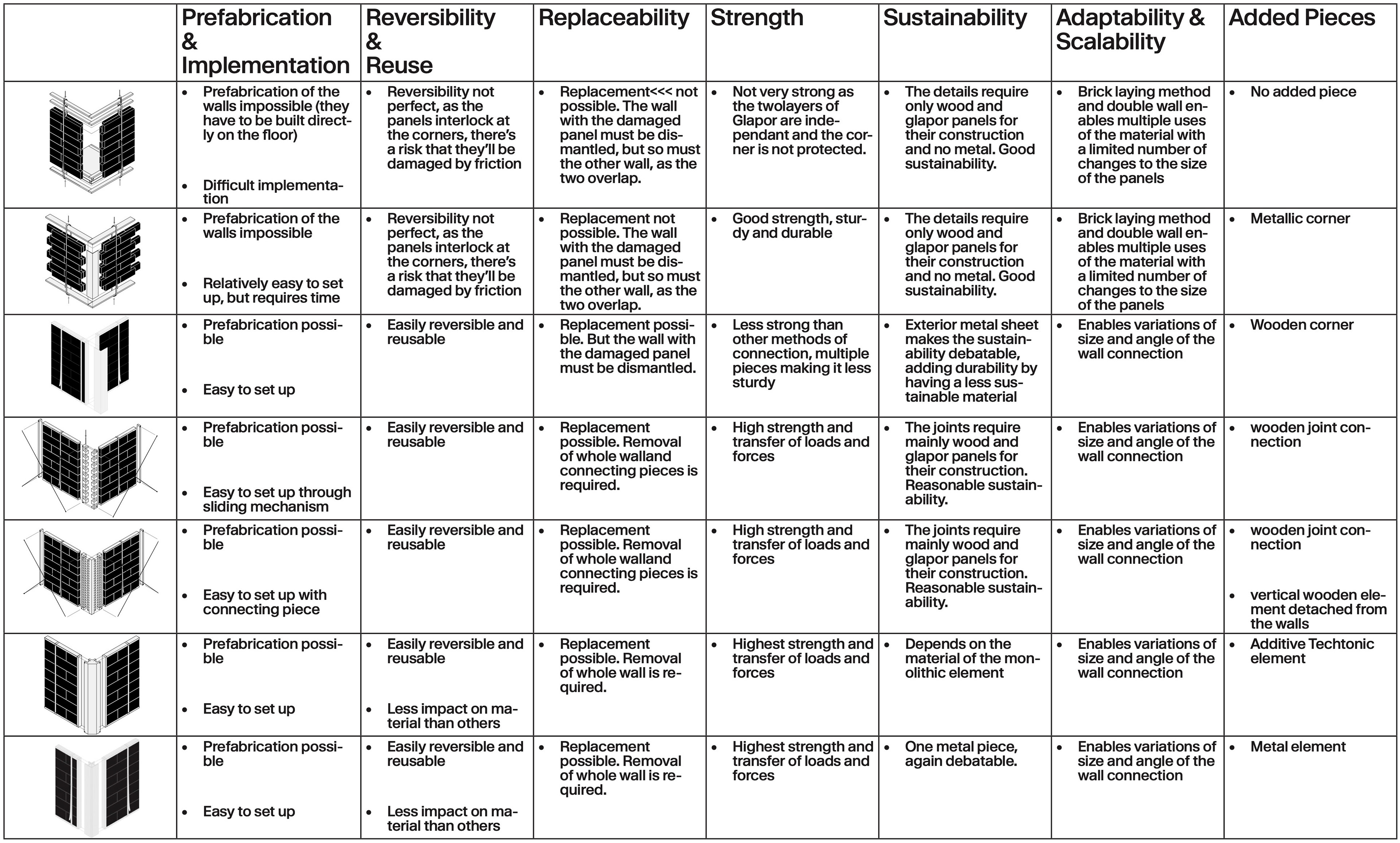
(7) Potential Pavillon
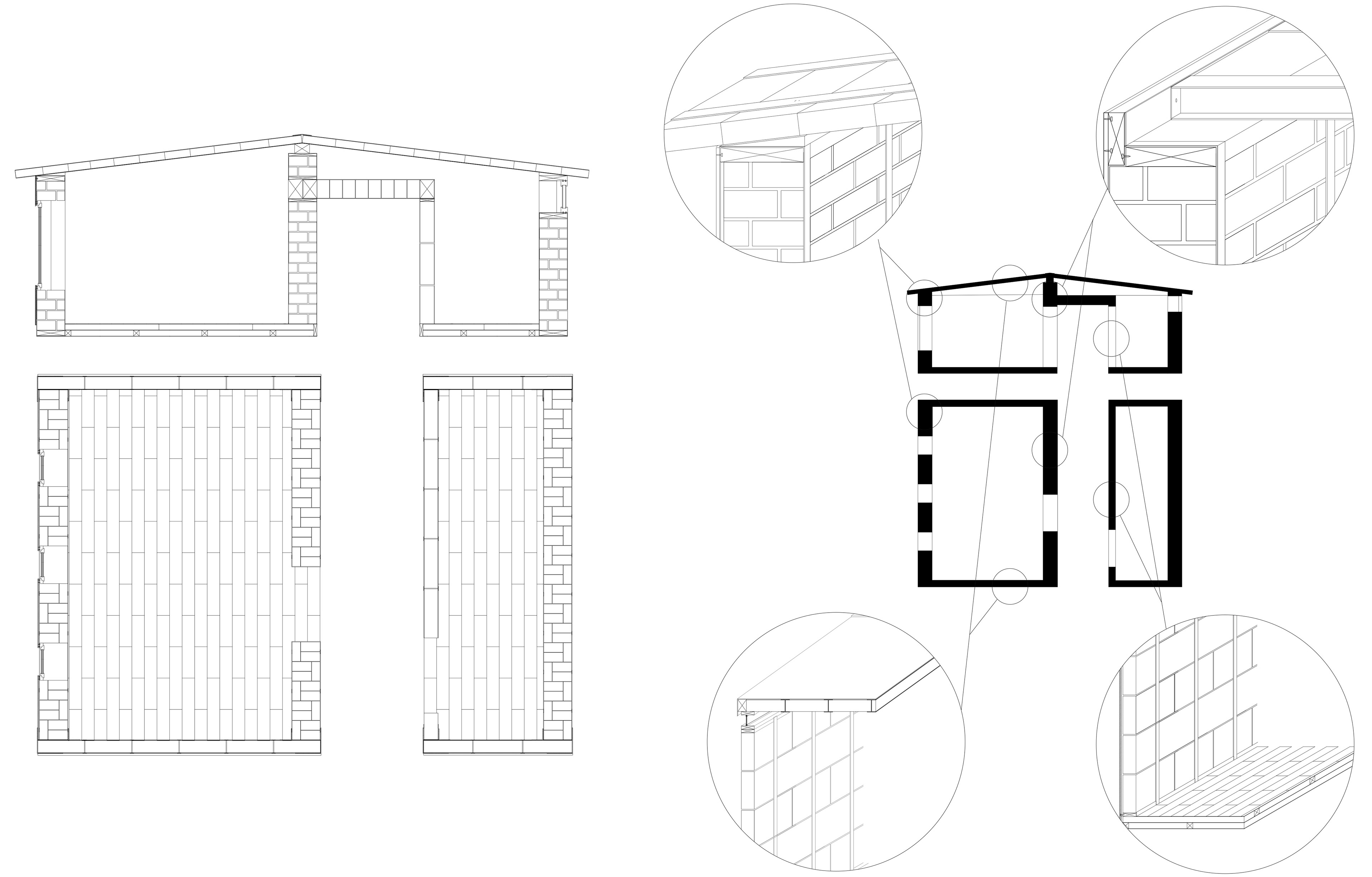
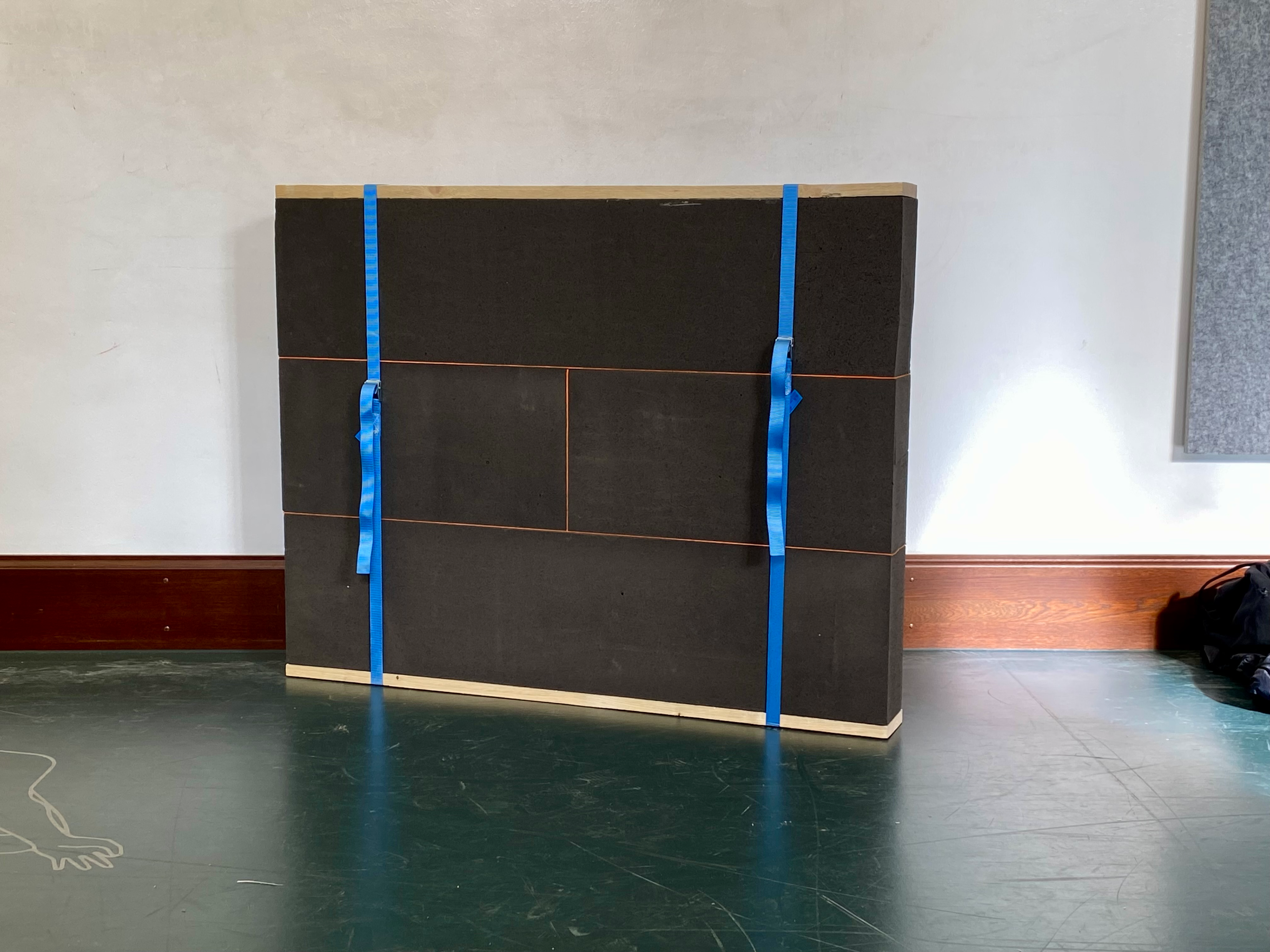
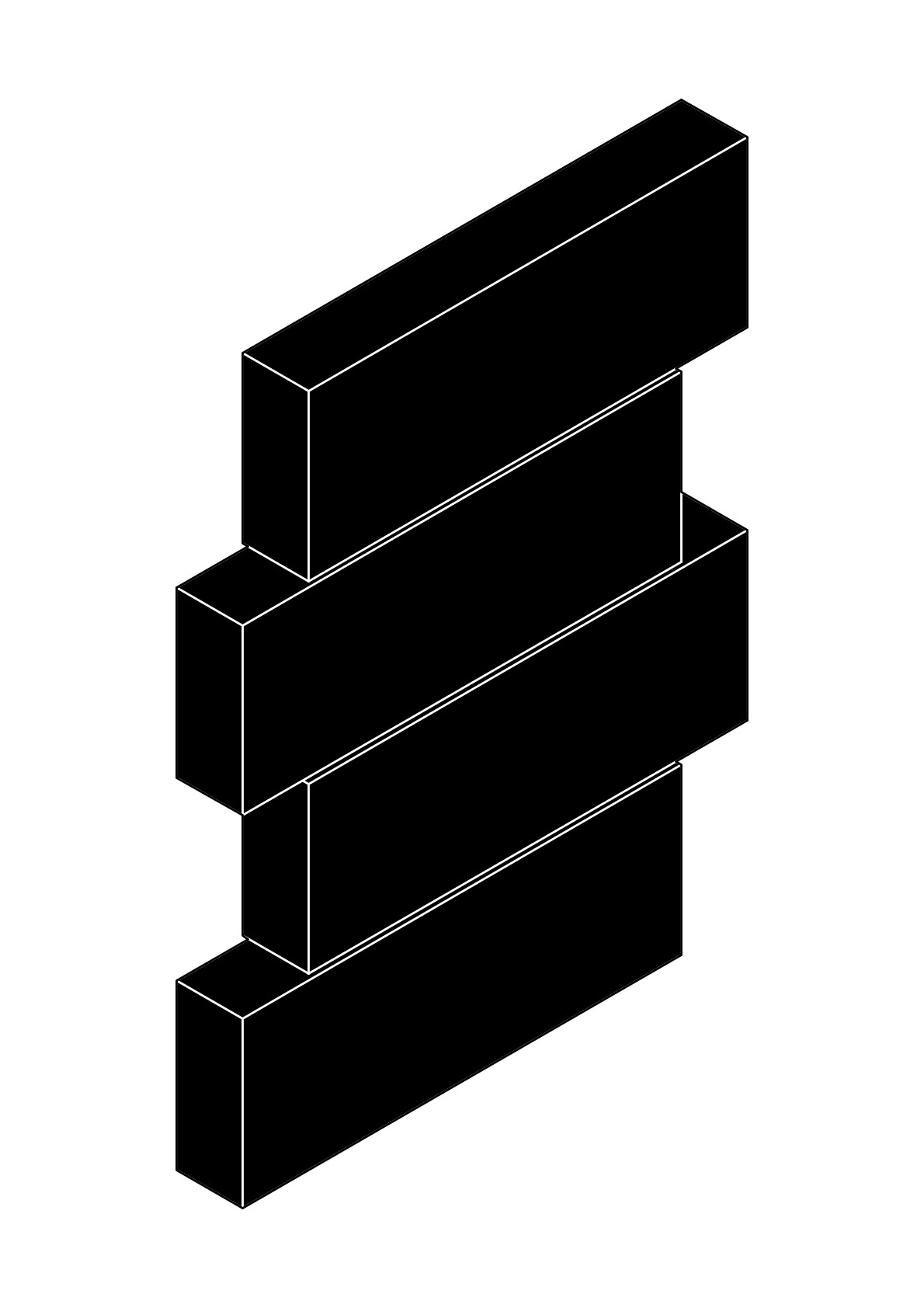
Louise Amstutz, Jonty Tolleson
for Project Re:Glas
Prof. Niklas Fanelsa and Viktoria Schweyer Benedikt Perotein, Studio PEIPEI
AND Professorship of Architecture and Design Wintersemester 23/24